Cada vez que se realiza un relevamiento energético del Sistema de Aire Comprimido, surgen recurrentemente dos temas claves considerados de máxima prioridad por el personal de planta: las fugas y las caídas de presión. Este artículo trata acerca de la importancia e injerencia de las segundas sobre la Eficiencia de una Red de Aire Comprimido.
Los beneficios de un control adecuado de la Presión en un Sistema de Aire Comprimido están comúnmente eclipsados por un concepto poco preciso que indica que “por cada 0,07 bar reducidos, puede generarse un ahorro energético de entre el 1 y 2%”. Sin embargo esta “regla de oro” ha sido malinterpretada, ya que sólo aplica para la clase de compresores cuya presión de descarga es de 6,9 bar (100 PSIG). Existen diferentes factores de multiplicación para otros valores de presión en relación a la demanda de energía y potencia.
De hecho, un control efectivo de la presión del sistema de generación de aire ofrece un potencial ahorro de energía considerablemente mayor al 1 ó 2% antes mencionado. A modo de ejemplo, un compresor de 100 HP que entrega 14,2 m3/min a 6,9 bar podrá ahorrar cerca de un 5% (5 HP) de potencia si la presión de descarga se disminuye a 6,2 bar. Utilizando esta “regla de oro”, el potencial ahorro anual asciende a los U$S 1.790 aproximadamente (considerando un costo de la energía de U$S 0,06 / kW/h a razón de 8.000 horas al año).
Si bien nadie se opondría a generar este tipo de ahorros si resultan prácticos y sencillos de implementar, la cuestión más importante a considerar durante la evaluación de potenciales oportunidades de mejora respecto a reducir la demanda de aire con foco en la presión del sistema, es la relación directamente proporcional existente entre la presión de alimentación a prácticamente cualquier proceso neumático y el consumo de aire de éste.
La regla de oro comparable a dicha relación también puede apreciarse en los sistemas presurizados a 6,9 bar (100 PSIG). Por cada 0,06 bar que desciende la presión del aire que alimenta al proceso, se reducirá el consumo entre un 0,9 y 1,0%; lo que trasladado a una disminución de 0,7 bar en un flujo de 14,2 m3/min de un compresor de 100 HP ahorra 1,4 m3/min representando, para un total de 8.000 horas de trabajo al año y un costo de U$S 0,06 / kW/h, un recorte en el costo energético de U$S 5.000 anuales.
Antes de profundizar en la temática diremos que la utilización de “reglas de oro” no resulta en el método más preciso, pero sin dudas es práctico. Debemos considerar que en muchas hojas de datos de ingeniería correspondientes a los fabricantes de compresores se informa el Caudal entregado con un gradiente de ± 5%, y la potencia con ± 3%. Se ha utilizado esta información como guía durante muchos años y los sistemas de medición confirman su veracidad.
Alimentar un proceso con una mayor presión de la necesaria ocasionará también un consumo de aire adicional, comúnmente denominado “demanda artificial”
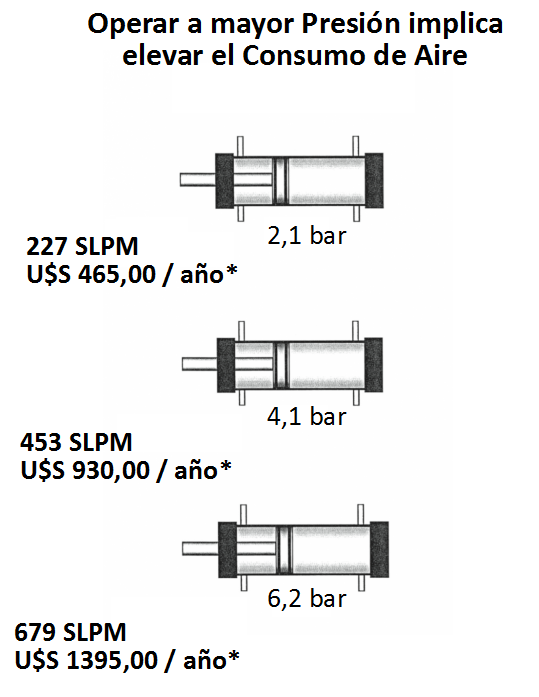
La Figura 1 ilustra cómo se comporta el Consumo de Aire en relación a la Presión de Alimentación para un cilindro neumático de 113 l de capacidad que opera a razón de 2 ciclos por minuto;
*Para calcular el costo se consideran 8.000 horas de trabajo anuales un valor de U$S 0,06 / kWh;
Consideraciones acerca de la Presión del Sistema de Generación de Aire
Se recomienda prestar especial atención a los siguientes aspectos:
- ¿La presión de los tramos principales de distribución (troncales) se mantiene estable durante los diferentes turnos de trabajo? En caso afirmativo, podemos considerar que el Sistema de Aire se encuentra correctamente balanceado; de lo contrario este aspecto debería ser tratado;
- ¿Se encuentra cada de unos de los procesos operativos neumáticos trabajando a la mínima presión de alimentación necesaria para una óptima productividad y calidad?;
- ¿Están actuando adecuadamente todos los Reguladores y Limitadores de Presión instalados?;
- ¿Es conocida la Caída de Presión existente entre el troncal principal y los diferentes procesos productivos que demandan aire?, ¿dicho gradiente se encuentra dentro de un rango aceptable? Si no fuera de esta manera, ¿dónde se localizan los causantes?, ¿qué presión requieren los procesos durante los lapsos de inactividad y mientras trabajan a plena marcha?;
También resulta de gran relevancia monitorear la presión en las bajadas de línea de distribución de aire que llegan hasta los diferentes puntos de uso: ¿desciende abruptamente cuando el proceso se inicia?, y lo que es más importante aún, ¿el diferencial de presión resulta excesivo durante el ciclo de funcionamiento normal de la aplicación? En caso positivo, estaríamos frente a un indicador de varias posibles causas, siendo lo más probable que dicha bajada de distribución resulte insuficiente para alimentar correctamente al proceso. Ahora bien, si la presión real medida en la alimentación al mismo es menor al valor tomado durante el lapso de inactividad en la bajada de distribución sin que por ello se vea perjudicada la productividad y/o calidad de la operación, podremos afirmar que este valor inferior de presión medida se acerca más a la presión óptima (mínima necesaria) de la aplicación, que a la presión establecida para el troncal principal.
Es aconsejable investigar todas las problemáticas que se pudieran ir presentando. Algunas correcciones en el sistema de distribución y/o de almacenamiento pueden permitir reducir de forma estable el valor mínimo de presión de línea, ocasionando ahorros muy significativos en el consumo de aire, sin mencionar además las mejoras relacionadas con la productividad y calidad de los procesos.
Caso de Éxito 1
En esta planta, el sistema principal de distribución de aire estaba configurado a 6,8 bar para abastecer a un proceso de molido de gran demanda. Al operar el mismo, la presión a la entrada caía hasta 4,3 bar a causa de un tramo de manguera de ⅜” demasiado extenso a través del cual se alimentaba la máquina. Esto ocasionaba serios contratiempos de productividad y calidad en el proceso, ya que descendía por debajo de los 6,8 bar la presión del troncal principal. Fue entonces que el personal de planta se propuso elevar dicho seteo hasta los 8,6 bar, lo que hubiese implicado un incremento en el consumo energético del compresor de entre el 11 y 12%. Finalmente, la solución para suprimir la notable pérdida de carga consistió en incrementar la sección de la bajada de línea que alimentaba el molino, reemplazando la manguera por cañería rígida de 1”.
Las correcciones realizadas sobre este tramo de la red de distribución hicieron posible operar el Molino de forma óptima a una presión medida y limitada a 5,2 bar, y reducir la presión general del Sistema de Aire a 5,9 bar. Mientras que la configuración original a 6,8 bar requería 1.500 HP de potencia de compresores, esta mejora permitió no sólo incrementar en un 30% la producción total, sino además disminuir la demanda de aire en 14,2 m3/min (ergo reduciendo en 100 HP la potencia consumida), aumentando también la productividad y calidad de los procesos neumáticos con un descenso del consumo de aire en los mismos. En términos numéricos, estos resultados se tradujeron en un ahorro de U$S 28.902 anuales y un aumento del 30% en los niveles productivos.
Reguladores y Limitadores de Presión adecuados
Se trata del asunto más significativo que podremos detectar en prácticamente cualquier relevamiento de planta. Los Reguladores y Limitadores de Presión son habitualmente seleccionados considerando únicamente las medidas de conexión (ej: ¾”), en lugar de analizar también el flujo de aire que permiten pasar a la mínima presión de entrada posible y la pérdida de carga admitida que pudieran ocasionar aguas abajo.
Los cilindros de doble efecto suelen ser una aplicación clave para detectar este tipo de inconvenientes; ya que habitualmente la línea que comunica al Regulador con la alimentación de los primeros resulta insuficiente para admitir el volumen de aire que demanda el cilindro durante su accionamiento, a la espera de que el Regulador habilite mayor presión. En este tipo de función con la que cuentan los Reguladores de Presión dinámicos, juega un papel importante el tiempo de respuesta y la disponibilidad de aire comprimido al cilindro durante el ciclo completo de trabajo, así como el valor de presión constante que pueda sostenerse en este último. Comúnmente, al darse la situación en la que la carrera del cilindro no llega a ser la adecuada, el operador actúa llevando la presión a un mayor valor o incluso habilitando toda la carga disponible en la línea, incrementando también de forma directamente proporcional el consumo de aire.

Algunos ejemplos de Pistolas que poseen nuestros clientes y fueron equipadas con Escudos de Protección contra Virutas y Boquillas de Soplado de Alta Eficiencia y Seguridad.
La Figura 3 señala un método para la corrección del inconveniente planteado – considerando previamente las características dinámicas del Regulador de Presión y el Cilindro, así como el volumen de aire necesario para completar el recorrido de este último – instalando un pequeño Separador Ciclónico con Reservorio de Aire dedicado para suministrar el caudal correcto al proceso, el cual se llena nuevamente cuando el Regulador de Presión abre. Asimismo el Separador Ciclónico no sólo actúa como pulmón de aire, sino que además retiene un gran porcentaje del particulado y humedad presentes en la línea (80% aprox), contando además con una purga de condensados de alta eficiencia sin consumo de aire. Otras soluciones aplicables al caso podrían ser: incrementar la sección de la línea de alimentación para que este volumen adicional pudiera alojar el aire que requiere la aplicación, o bien reemplazar el Regulador de Presión por otro de perfil más acorde al cilindro sobre el que actúa. Como norma general toda mejora deberá estar orientada a abastecer los procesos con el mínimo caudal de aire necesario a la menor presión estable posible. Nuevamente, si estas correcciones son monitoreadas e implementadas adecuadamente, se elevará la productividad y calidad de las aplicaciones, mientras que el consumo de aire se acercará cada vez más a su valor óptimo.

Conclusiones
Este tipo de proyectos de mejoras mencionados, cuando son llevados a cabo con éxito, devuelven resultados muy satisfactorios en materia de reducción de consumos de aire comprimido con un costo de inversión relativamente bajo. En términos generales, en un sistema de presión de descarga de 6,9 bar, la mayoría de los procesos tendrán una presión de alimentación idónea de entre 4,8 y 6,2 bar. Si alguna aplicación demandara una carga mayor, probablemente sea aconsejable considerar la instalación de un Amplificador de Presión, o bien se requerirá elevar la presión en la línea principal de distribución.
Factores claves a considerar para un adecuado Control de la Presión del Sistema de Aire:
- Mínima Presión Efectiva que requiere cada proceso;
- Posibilidad de garantizar dicha presión de forma estable y controlada;
- De ser posible, monitorear la presión en cada punto crítico de los procesos;
- Búsqueda permanente de oportunidades de mejora para reducir los consumos de aire;
Ante preguntas o comentarios, por favor, comuníquese con el Departamento de Ingeniería de AYRFUL:
Tel.: (011) 7700-0280 Rot.
Email: ingenieria@ayrful.com.ar
Web: www.ayrful.com.ar