Una Empresa líder dentro del sector de Panificados no sólo garantiza que todas sus plantas fabrican productos horneados de alta calidad de forma productiva y rentable, sino que además optimiza y gestiona sus utilidades para preservar energía y proteger al medioambiente.
Los esfuerzos de la Compañía han conseguido, además de aumentar la rentabilidad y alcanzar la sustentabilidad medioambiental, obtener gran reconocimiento mediante la Certificación Energy-Star® que otorga la Agencia de Protección del Medioambiente.
El Ingeniero responsable de la Gestión Energética, Salud Corporativa, Seguridad y Medioambiente de la Empresa comentó que se trataba tan sólo de una cuestión de tiempo hasta que la Compañía se adjudicara la certificación para sus varias plantas productivas.
“Cumplimos los requisitos que exige la Certificación Energy-Star® durante muchos años gracias a nuestro Programa de Gestión Energética proyectado a largo plazo y las mejoras realizadas en materia de Eficiencia, pero decidimos adoptar una estrategia más enfocada en las Mediciones de los Consumos Energéticos, especialmente los relativos a los Sistemas de Aire Comprimido, dado que allí detectamos un enorme potencial para el Ahorro de Energía”.
Aire Comprimido: un servicio clave en la fabricación de Panificados
Los productos de la compañía se producen en más de 50 establecimientos a través de todo el mundo, e incluyen alimentos tales como panes de molde, piononos, rosquillas, bizcochuelos y galletas.
El horneado de los panificados se lleva a cabo en instalaciones que van desde los 4.645 a los 18.580 m2. Habitualmente, las fábricas operan las 24 horas del día durante la semana completa alternando con la producción, las actividades de mantenimiento y sanitización.
La empresa se vale del aire comprimido para alimentar controles neumáticos y cilindros que se utilizan en prácticamente todas las etapas productivas, ya sea para el transporte de materiales, la aplicación de coberturas sobre panificados, la generación de vacío con el cual se alimentan las ventosas para la manipulación de bandejas y productos, o la vibración neumática que forma parte del proceso de tamizado de los materiales en polvo, sólo por nombrar algunas de las aplicaciones principales.
Antes de que la compañía tomara la iniciativa de mejorar la Eficiencia del Aire Comprimido, un Sistema de Generación y Tratamiento típico de planta consistía de tres compresores de tornillo rotativo de transmisión directa, cada uno con un motor de 75 HP capaz de generar 8,5 m3/min a 8,6 bar. Cada sistema incluía también secadores y filtros para obtener un aire limpio y seco de la más alta calidad. Sin embargo, esta estructura comenzaría pronto a cambiar.

El Enfoque Holístico comienza por la evaluación de los Sistemas
En virtud del compromiso asumido por la Empresa hacia la Mejora Continua, se adoptó un enfoque global para la reducción de los costos energéticos generados por los sistemas de aire comprimido; buscando obtener no sólo ahorros de energía, sino también un incremento de la productividad y la confiabilidad, así como la reducción de los desechos producidos.
El proceso de mejoras en la Red de Aire comenzó con la recolección de datos y la evaluación de los sistemas existentes, lo que incluyó:
- Una inspección de la carga de aire comprimido en cada planta y sus diversas aplicaciones;
- La identificación de inconvenientes en cada sector, tales como puntos de embotellamiento y potenciales procesos poco confiables;
- Mapeo del flujo, presión y potencia eléctrica consumida del sistema de aire comprimido, a fin de identificar oportunidades de mejora;
- Análisis de la red de distribución de aire y sus componentes;
La Auditoría también involucró explorar todo tipo de opciones de mejora, incluyendo la posibilidad de acceder a tarifas más bajas para las utilidades locales con la implementación de programas de gestión de la demanda y sus respectivos incentivos. Previo a ejecutar cada inversión, se tuvo en consideración la tasa arancelaria para una determinada línea o planta productiva y se evaluó si la operación bajo una tarifa diferente resultaría finalmente más económica; ya que, en última instancia, ahorrar energía no necesariamente implica siempre abaratar costos.
Mejoras exhaustivas para el Sistema de Aire Comprimido
De acuerdo con los resultados que arrojó la Auditoría, los equipos de Ingeniería definieron ciertos sectores con mayor potencial de mejora y llevaron adelante allí una serie de actualizaciones a la Red de Aire.
Entre las principales iniciativas existentes en la Industria de Panificados se halla la orientación a reducir la demanda artificial, la cual se conforma de todos los consumos innecesarios que incrementan la carga de los compresores aguas arriba, y se suman al caudal real de aire que requieren las aplicaciones neumáticas de planta. En muchas empresas, dicha demanda ocurre debido a la tendencia que poseen a evitar inversiones de capital, y de tal forma, la eficiencia del equipamiento no siempre se tiene en consideración al momento de la compra de la unidad.
En este caso, la Empresa realizó una serie de mejoras sobre los componentes de los sistemas de aire, con el fin de reducir la demanda artificial:
- Incremento de la sección de las cañerías con el fin de disminuir las restricciones al flujo de aire;
- Agregado de pulmones en áreas alejadas o de cañerías más reducidas;
- Actualización de las purgas de condensado temporizadas instaladas en pulmones y filtros por las del tipo Capacitivas Electrónicas con sensor de nivel, para eliminar así un consumo de aire dispensable;
- Instalación de Manómetros Diferenciales en los filtros de aire para determinar con precisión cuándo deben ser reemplazados los cartuchos filtrantes en pos de aumentar la eficiencia del aire comprimido y disminuir el consumo energético;
- Localización y reparación de las fugas causadas por todo tipo de factores, desde aquellas generadas a través de pequeños orificios en cañerías corroídas hasta conexiones con la junta deteriorada o inclusive ausente;
Además, la compañía fue incluso más lejos en la reducción de la demanda artificial al generar ahorros de energía en otros aspectos sustanciales, tales como el uso de los compresores de aire para bajar el consumo energético; donde fue posible, se integró un sistema de recuperación de calor al circuito de enfriamiento del aire comprimido, aprovechando el calor recuperado en varios procesos, como la calefacción de ambientes.
Mejor Control del Sistema de Aire Comprimido
Otra de las serie de mejoras que se implementaron dentro del enfoque holístico que se le dio al Proyecto involucró los métodos de control y operación de los compresores de aire del sistema.
Anteriormente, la mayoría de las plantas operaban con dos compresores de velocidad fija a casi plena carga durante tres turnos completos para cubrir la demanda de aire de los procesos. Adicionalmente, un tercer equipo trabajaba a plena capacidad o se desconectaba, durante aproximadamente 30 minutos por cada hora de producción. También éstos eran requeridos para proveer baja presión durante los momentos en que se detenía la producción y se llevaban a cabo las tareas de sanitización y mantenimiento.
Las plantas normalmente operaban los compresores en modo continuo utilizando un esquema de control en cascada. Sin embargo, esto implicaba trabajar con puntos de ajuste en cascada en rangos de 0,7 bar, de forma tal que los primeros compresores en arrancar trabajaban con elevada presión para sostener el esquema de control. Éste fue uno de los factores que se decidió mejorar.
Debido a las notables oscilaciones de presión que acusan los sistemas de aire, bajo el esquema anterior se podría tener a un compresor intentando ponerse en marcha y apagarse al mismo tiempo, generando que la unidad eventualmente falle, dado que está contemplada una cantidad limitada de arranques por hora que estos equipos deberían efectuar. Adicionalmente, se genera un gran consumo de energía cuando los tres compresores trabajan con poca carga.
Para mejorar la fiabilidad y ahorrar energía, cada planta convirtió uno de sus tres compresores de velocidad fija en una unidad VSD, con variador de velocidad. Asimismo, el controlador del sistema ahora iguala dinámicamente el caudal de aire generado con la demanda del servicio, operando únicamente las unidades necesarias. Típicamente, los dos equipos de velocidad fija proveen la carga básica de la red, mientras que el compresor VSD actúa equilibrando los requerimientos variables de aire durante la producción. Las plantas también utilizan la unidad VSD durante las jornadas no productivas para proveer aire comprimido donde y cuando se hace necesario, dejando muy clara la relevancia y las ventajas de este tipo de tecnología.
La importancia de los Secadores Cíclicos con Refrigerante de Masa Térmica
Además de la implementación de la tecnología VSD para los compresores de aire (así como para otros equipos), se propusieron los secadores cíclicos con refrigerante de masa térmica donde aplicaran para los sistemas de aire comprimido.
Antes de que la empresa efectuara mediciones de la eficiencia del aire comprimido, se utilizaban secadores desecantes complementados por filtros para entregar a la red un aire de alta calidad. No obstante, éstos fueron sustituidos por los equipos refrigerantes mencionados en varias de las plantas debido a las oportunidades de ahorro energético que ofrecen.
Esto se debe a que con el uso de un secador desecante, aproximadamente un cuarto del caudal de aire generado se utiliza para secar el medio, algo que podría considerarse una gran fuga de aire “intencional”. Si bien, las prestaciones y características de un secador por adsorción pueden resultar muy adecuadas en algunos casos, no conforman la mejor elección ante cargas variables como las del caso de estudio. Asimismo, es difícil no apreciar el ahorro generado por el uso de secadores cíclicos con refrigerante de masa térmica dado que sus motores trabajan a demanda de las necesidades y utilizan un medio de almacenamiento de energía fría para secar el aire comprimido.
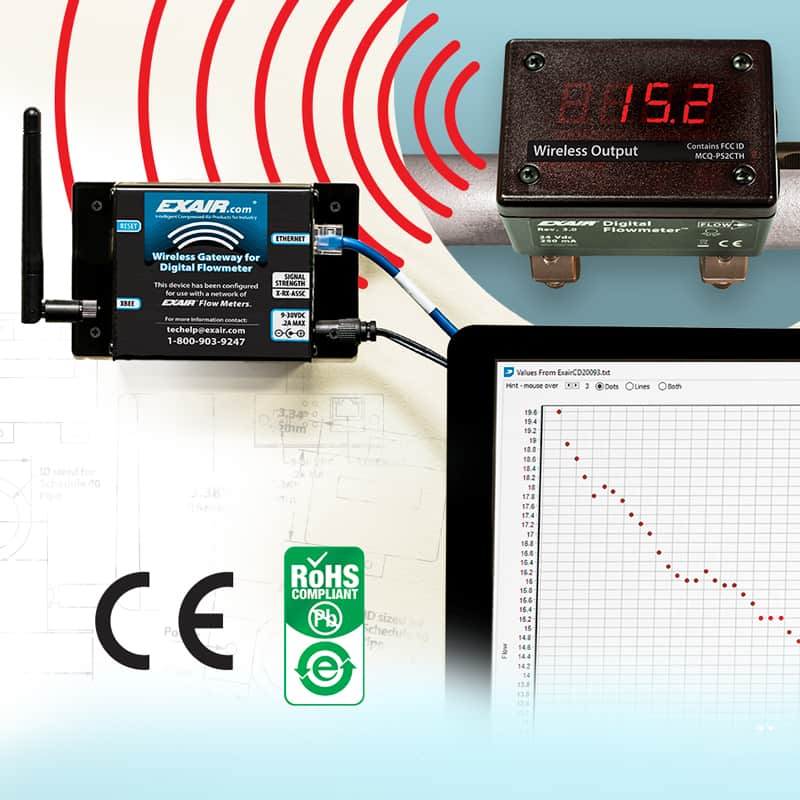
Para dejarlo en claro, estos secadores resultan especialmente eficientes en sistemas de aire de carga variable dado que el medio no se enfría directamente por el uso deliberado del compresor de refrigerante, sino por intercambio de temperatura con un fluido de masa térmica especial. A modo de ejemplo, una mejora de este tipo permite eliminar un compresor de 100 HP de un sistema de generación compuesto por cinco equipos con la misma capacidad, ya que el caudal que generaría sería utilizado para cubrir la demanda del secador desecante durante el proceso de regeneración; lo que significa un enorme ahorro de energía.
Retrocediendo hasta el troncal de distribución principal de la red de aire, el sistema de mangueras que alimentaba la herramienta consistía de un conjunto de cuatro acoples rápidos estándar de ¼” ubicados en varios puntos y un tramo de 15 m de manguera de diámetro interno ¼” montado sobre un enrollador. Dicha longitud de tubería flexible es necesaria para proveer una adecuada movilidad y alcanzar toda la extensión de los grandes moldes que allí se ubican. Así fue que, mediante los cálculos pertinentes, se confirmó el diferencial de presión estipulado para esta disposición: el sistema de distribución por manguera estaba sub-dimensionado.
El Equipo de Ingeniería, responsable de las mejoras descritas, continúa trabajando en todas las instalaciones de la Empresa para la implementación de nuevas actualizaciones orientadas al Ahorro de Energía de forma integral a todos los sistemas de las plantas. Ya sea que se trate de una red de aire comprimido, un sistema de enfriamiento, o cualquier otro gran consumo energético, la mejora debe siempre partir del planteo correcto cuando se trata de inversión de capital y costos operativos.
Cuando se planea la adquisición de cualquier nuevo equipamiento para las plantas, los autores de este Proyecto recomiendan optar por el sistema más eficiente, basándose en el menor costo relacionado a la escala de tarifas de los servicios públicos involucrados y los reembolsos vigentes a los que pueden acceder, así como también se considera el costo operativo aparejado.
Todo indica entonces que la Compañía continuará siendo un gran ejemplo de cómo los fabricantes de panificados a gran escala pueden disminuir sus costos energéticos manteniendo la rentabilidad y confiabilidad en la manufactura de alimentos horneados de alta calidad.
FUENTE: https://www.airbestpractices.com/industries/food/weston-foods-achieves-energy-star-certification-commitment-sustainability
Ante preguntas o comentarios, por favor, comuníquese con el Departamento de Ingeniería de AYRFUL:
Tel.: (011) 7700-0280 Rot.
Email: ingenieria@ayrful.com.ar
Web: www.ayrful.com.ar